
TPU, short for thermoplastic polyurethane, is a versatile thermoplastic elastomer (TPE) widely utilized in automotive, transportation, aerospace, sports, and medical industries. Its unique blend of plastic's durability and rubber's elasticity makes TPU perfect for flexing or compressing applications.
What is TPU 3D Printing Material
TPU or thermoplastic polyurethane, is one of the unique polymers in the polymers family. It has many properties like elasticity, abrasion and heat resistance. It can also be used as a substitute for rubber in many applications. TPU is already being used at a massive scale in the sports Industry and has also found a way in automotive as well as healthcare. TPU is an ideal material for 3D Printing applications that want similar properties of rubber.
TPU, or Thermoplastic Polyurethane, is a flexible and durable plastic used in 3D printing. Unlike the rigid PLA, TPU is known for its elasticity and softness. This makes it ideal for creating objects like phone cases, shoe soles, and even prosthetic limbs. TPU's flexibility and resistance to abrasion make it an excellent choice for applications where toughness and flexibility are essential. It's a favorite among 3D printing enthusiasts looking to produce items that need to withstand bending, stretching, and impact
How Are TPU Parts Made?
TPU products play a ubiquitous role in our daily lives due to their widespread use and popularity, particularly in mass production facilitated by traditional injection molding processes. Despite its cost-effectiveness for producing parts in large quantities, injection molding does have limitations in terms of geometric flexibility and customization. Products commonly perceived as rubber are often made of TPU.
​
While injection molding is suitable for standardized production in quantities ranging from hundreds of thousands to millions, certain industries, such as medical device manufacturing or sporting goods, seek alternatives that offer greater flexibility for low-volume production or customization. The constraints of mass production also pose challenges for small businesses and startups, impeding their ability to bring products to market swiftly, as they depend on large industrial injection molders for external production.

Why 3D Print With TPU Material?
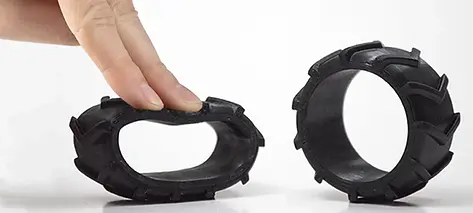
Utilizing 3D printing technology with TPU and TPE materials opens up innovative possibilities beyond conventional workflows. This approach proves invaluable for creating intricate parts, embracing personalized designs, facilitating swift iteration and design processes, and achieving cost-effective low-volume production.
​
TPU 3D printing offers diverse options, with popular techniques including fused deposition modeling (FDM) and selective laser sintering (SLS). The continuous evolution of 3D printing technology and materials has led to a substantial increase in the number of manufacturers seamlessly integrating this methodology into their production processes.
​
The advantages of TPU 3D printing extend to shorter iterative cycles, particularly beneficial for rapid prototyping applications, and the ability to customize end-use part production. In industries where traditional outsourcing is common, especially during mass production manufacturing phases, 3D printing contributes to an enhanced and vertically integrated end-to-end workflow.
​
In applications where TPU and rubber find frequent use, such as protective devices like helmets or orthotics and insoles, 3D printed TPU parts prove ideal for mass-customized helmet paddings, orthotics, sports equipment, goggles, headsets, or ergonomic gripping components for tech products.
Applications of TPU 3D Printing
There are many traditional manufacturing workflows are effective for TPU parts, especially for mass production. Yet, 3D printing TPU offers a compelling alternative, particularly in scenarios requiring speed, ease, rapid prototyping, on-demand manufacturing aids, and customization. From quick prototypes in the design phase to end-use parts and mass-customized consumer goods, 3D printed TPU accelerates workflows without compromising mechanical properties or fidelity.
Rapid Prototyping
3D printing with TPU empowers businesses to handle prototyping in-house, reducing lead times and costs compared to external services. For example, designing a sports helmet involves creating both a hard shell and soft cushioning. TPU is an ideal material for this, and its flexibility allows for innovative lattice structures and impact negation technology.
​
Traditional tooling methods become costly when experimenting with new designs, and outsourcing to design bureaus takes too long. Using one workflow and technology for both the hard outer shell and soft inner cushion accelerates the iteration process. For extensive physical testing of helmets, multiple cushioning pads are required, making in-house 3D printing, specifically with Fuse Series SLS 3D printers and TPU 90A Powder, a cost-effective solution.
​
The Fuse Series workflow offers versatility by allowing adjustments in design, such as wall thickness variations, to produce parts with different hardness levels for various applications or after testing iterations. With access to multiple materials and mechanical properties, this in-house approach streamlines development and manufacturing, providing a reliable platform for prototyping using TPU 90A Powder with the Fuse Series.

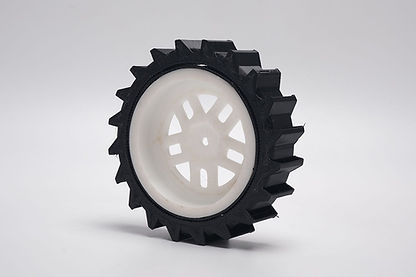
Automotive sector
In recent years, the 3D printing market has witnessed the introduction of numerous compelling high-performance 3D materials, boasting properties typically associated with injection molding. These cutting-edge materials not only fulfill the stringent demands of industries, particularly in automotive, but also open up innovative possibilities. TPU (Thermoplastic Polyurethane) 3D printing material, renowned for its flexibility, has found application in the automotive sector for crafting various components. Beyond car interior elements, it is utilized for manufacturing air filter covers, bellows gimbals, and other flexible and durable parts essential in the car development process.
Medical Devices
3D printed TPU is a durable and tough material, ideal for medical applications like prosthetics, orthotics, and devices. Its flexibility and strength allow for the creation of custom, resilient parts, combining the advantages of rubber materials with SLS 3D printing. TPU suits various medical uses, including prototypes, orthotic pads, wearables, and splints. This innovation expands possibilities in healthcare 3D printing, meeting safety and strength requirements, providing a valuable tool for medical professionals.

Physical and Mechanical Properties of TPU 95 A
* The above properties may be subject to change depending upon the material grade availability.