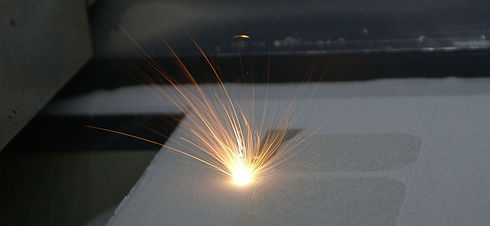
SLS
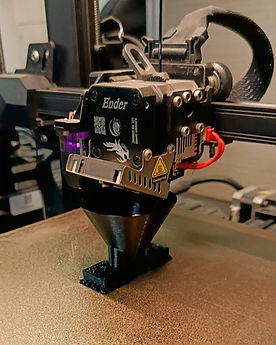
FDM
SLS vs FDM : Comparative Analysis of Two 3D Printing Technology
3D printing and Rapid prototyping have made significant progress in recent years, transforming the way of creating prototypes, products, and complex designs that would not be possible without traditional manufacturing methods. In this article, we compare the analysis between Selective Laser Sintering (SLS) and Fused Deposition Modeling (FDM) 3D printing as well as their processes, applications, advantages, and limitations
THE SLS PROCESS
Selective laser sintering (SLS) is a powder-based manufacturing technology in which materials are fused together using a laser. This method begins with the deposition of thin layers of powder that is applied to a build platform, followed by the precise application of the laser, which selectively sinters and solidifies the particles into the desired shape.

THE FDM PROCESS
Fused Deposition Modeling (FDM), also called Fused Filament Fabrication (FFF), is another 3D printing process that has become popular day by day, especially for private use. FDM operates by heating thermoplastic filaments such as PET-G, ABS, TPU, or various composites to their melting temperatures. These materials are extruded through a nozzle onto a build platform layer by layer


This is PLA filament used for FDM 3d printing technology

This is nylon powder used in SLS 3d printing technology

TPU material for FDM 3d printing technology

This is PLA filament used for FDM 3d printing technology
Material Diversity
FDM printing gives you lots of filament options, offering a rainbow of colors that really stand out next to SLS materials. This gets hobbyists pretty pumped because they can make all sorts of colorful 3D prints. Plus, most of these filaments are budget-friendly, which is great for folks doing projects at home or running a small business. Handling and storing them is a breeze, and you can use them for loads of different things. But, there's a downside: FDM prints aren't as strong as ones made with powder-based methods. That's because FDM printers work at lower temperatures, which can make the printed stuff less resistant to heat.
Level of Detail
One of the main advantages of Selective Laser Sintering (SLS) is the high level of detail achieved through the precision of the laser and the thin layers of thickness of the material deposited. This precision results in parts with superior surface finishes, intricate designs, and can be reproduced more accurately due to low tolerances. In contrast, the nozzle through which the filament is extruded is limited to the smallest possible diameter and does not offer the precision of the laser, resulting in a coarser and rougher surface quality.


Describe your image

Describe your image


Describe your image

Describe your image

Describe your image

Describe your image
Support Structures
Unlike FDM printing, SLS printing needs support structures as the unsintered material itself as a supportive structure. Furthermore, the unused powder is also recyclable up to 90% (depending on the material) and can be reprocessed into new printing powder by adding fresh powder. The support structures needed for FDM printing to create overhangs and more intricate geometries, on the other hand, cannot be reused after printing and ends up as waste. The points at which the support structures have to be removed further reduce the surface quality of the parts.
Mechanical properties
Compared to FDM, SLS demonstrates notable advantages at the material level. It's the higher melting temperature of polymers with higher melting temperatures, such as PA12 with a melting point of 185°C, and makes the printed parts more heat resistant. This turn opens the door to a wide range of applications, particularly those subjected to thermal stresses. Moreover, SLS powders offer greater options regarding mechanical properties, such as high tensile and compressive strengths, which are more challenging to achieve in the FDM process. These superior mechanical properties are clear for SLS, even metal powders utilizing innovative techniques like Cold Metal Fusion.


Describe your image

Describe your image

Applications for SLS
SLS and FDM are two cool methods for making stuff. SLS is great for making intricate and useful parts used in lots of industries like aerospace, cars, and healthcare. It's also awesome for quickly making prototypes of fancy designs and small batches of things like custom shoe inserts. On the other hand, FDM isn't as good for making lots of parts at once, so it's slower and usually not the best choice for making things in big batches.
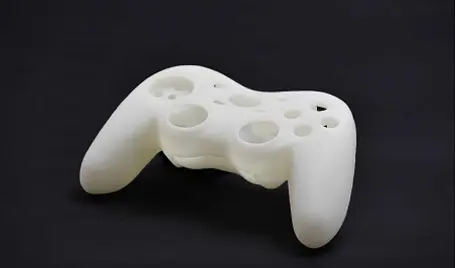
Applications for FDM
Due to its ease of use and lower price, FDM has become highly accessible to hobbyists and small-scale enterprises who want to implement their concepts quickly and cost-effectively. This technology is well suited for first iterations in rapid prototyping and is used in product design, architectural design, and artistic creation. Additionally its industrial applications, FDM serves as an invaluable tool. FDM can act as a bridging technology to test concepts before printing them through cost-intensive processes.
.jpg)
SUMMARY
SLS and FDM stand out as robust 3D printing methods, each boasting unique attributes and drawbacks. Deciding between them hinges on project-specific needs.
When prioritizing material properties, SLS emerges as the preferred choice for crafting prototypes, end products, and even small to mid-sized series with exceptional quality and functionality. However, SLS systems often pose a financial hurdle for hobbyists due to their steep initial costs and pricey materials.
Alternatively, for endeavors where material properties take a back seat, FDM shines with its diverse array of vibrant filaments and affordable entry point, making it an ideal platform for individuals, small businesses across sectors, and educational institutions.
In essence, the landscape of 3D printing, particularly with SLS and FDM, promises to propel innovation forward, enriching their utility across various domains. Anticipated advancements are poised to further enhance the already remarkable performance of these techniques, ushering in fresh possibilities within the manufacturing
