SLS 3D printing for the automotive industry
The automotive sector has always been a pioneer in embracing technological progress, consistently exploring inventive methods to enhance manufacturing processes and vehicle capabilities. Over the past few years, a groundbreaking innovation called 3D printing, also referred to as additive manufacturing, has revolutionized the landscape of the automotive industry. This state-of-the-art technology enables the fabrication of three-dimensional objects through the sequential deposition of materials layer by layer, fundamentally reshaping the approach to car design, prototyping, and production.

Advantages of 3D Printing in Automotive Manufacturing
The integration of 3D printing technology within the automotive sector presents a myriad of advantages, positioning it as a valuable asset for manufacturers. Among its primary benefits is the expeditious prototyping process it enables. Unlike traditional methods which are time-intensive and expensive due to the necessity of specialized molds and tooling, 3D printing allows automotive designers and engineers to swiftly translate digital designs into physical prototypes. This rapid prototyping capability facilitates iterative refinement, ultimately accelerating the product development cycle and enhancing market competitiveness.
Moreover, the adoption of 3D printing translates into cost efficiencies within automotive manufacturing. By circumventing the complexities of tooling and minimizing material wastage, manufacturers can optimize production expenses. 3D printers utilize materials judiciously, constructing objects with precision and minimizing excess, thereby reducing overall costs. As the accessibility and affordability of 3D printing technology increase, its integration within automotive manufacturing becomes more feasible for both major industry players and smaller entities.
A significant advantage of 3D printing lies in its capacity for design flexibility. Traditional manufacturing methods often impose limitations on design complexity and customization. However, 3D printing empowers designers to create intricate and highly personalized components with ease. This newfound freedom enables exploration of innovative shapes, structures, and functionalities that were previously unattainable. Consequently, automotive manufacturers can leverage 3D printing to enhance vehicle performance, optimize aerodynamics, and integrate complex features, thereby improving overall efficiency and functionality.
Subsequent sections will delve into the various types of 3D printers commonly utilized in the automotive industry, examining their specific applications, advantages, and compatible materials. Additionally, the discussion will encompass the pivotal role of 3D printing in facilitating rapid prototyping, design optimization, customization, and supply chain efficiency within automotive manufacturing. Finally, recent advancements in 3D printing technologies will be explored, along with speculation on its future trajectory within the automotive sector
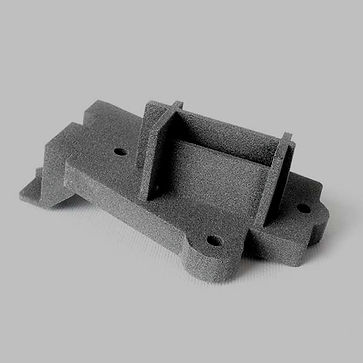
Why does the automotive industry need 3D printing?
The automotive industry benefits significantly from 3D printing (also known as additive manufacturing) due to several reasons:
-
Rapid Prototyping: 3d printing allows automotive companies to quickly iterate and prototype new designs. This rapid prototyping capability accelerates the development cycle, reduces time to market, and enables faster innovation.
-
Design Freedom: Unlike traditional manufacturing methods, which often have limitations in terms of complexity and geometries, 3D printing offers virtually unlimited design freedom. This enables engineers to create highly intricate and optimized components that are lighter, more efficient, and perform better.
-
Customization: 3D printing enables customization at scale, allowing automotive manufacturers to tailor products to specific customer requirements. This customization can range from personalized car parts to entire vehicles designed for individual preferences or niche markets.
-
Cost Reduction: While initial setup costs for 3D printing can be high, the technology offers significant cost savings over time, particularly in the production of low-volume or specialized parts. By eliminating the need for tooling and reducing material waste, 3D printing can lower overall manufacturing costs, especially for complex components.
-
Supply Chain Flexibility: Additive manufacturing reduces reliance on traditional supply chains by enabling on-demand production closer to the point of use. This reduces lead times, inventory costs, and supply chain risks associated with sourcing components from distant suppliers.
-
Light weighting: Weight reduction is critical for improving fuel efficiency and performance in vehicles. 3D printing allows automotive manufacturers to produce lightweight yet strong components by optimizing designs and using advanced materials, such as high-performance polymers and metal alloys.
-
Sustainability: Additive manufacturing generates less waste compared to subtractive manufacturing methods, where material is removed from a solid block. Additionally, 3D printing enables the use of recycled materials and promotes the adoption of more sustainable manufacturing practices in the automotive industry.
-
Innovation and Complexity: 3D printing enables the production of complex geometries and integrated assemblies that are difficult or impossible to manufacture using traditional methods. This encourages innovation in product design and engineering, leading to the development of next-generation automotive technologies.
Impact of 3D Printing on the Automotive Industry
As 3D printing technology emerged in the automotive sector, its initial application was primarily in the production of prototypes to assess fit and form. However, as the technology advanced and became more integrated into the automotive industry, newer and more robust applications, such as Fused Filament Fabrication (FFF), began to emerge. FFF technology enables the production of actual automotive end parts rather than just prototypes.
​
The utilization of 3D printed car components has the potential to significantly impact the automotive industry, potentially leading to a substantial increase in global automotive sales. According to the Global Automotive Outlook 2017, this could result in an additional 114 million in sales annually by the year 2024. This projection is significant, especially considering the limited number of Original Equipment Manufacturers (OEMs) that currently dominate this market.
​
Conversely, the automotive parts industry presents a different landscape, characterized by a dense and diverse ecosystem comprising thousands of players ranging from small to large-scale enterprises. Competition within this sector is intensifying with each passing day, with market projections estimating a value of approximately 17 billion USD by the conclusion of 2025.
​
Furthermore, Machine Design has forecasted a significant increase in 3D printing consumption by the automotive industry, with expenditures expected to reach 530 million USD by the conclusion of 2021. This indicates a growing reliance on additive manufacturing technologies within the automotive sector, reflecting a broader trend towards innovation and efficiency in production processes.
Core Application of 3D Printing in the Automotive Industry
Communication of Design and Concept
The utilization of intricate and precise 3D-printed models for concept and design communication within the automotive industry remains a seldom-explored avenue. While computer-aided design (CAD) models are prevalent, they often lack the depth necessary to pinpoint design issues effectively. Additionally, such models find frequent application in aerodynamic testing for newly developed vehicle models.
Customised Parts
Additive manufacturing is frequently employed within the automation sector to tailor the production process of components according to specific requirements, such as variations in drivers or vehicle types.
Validating Prototypes
In the automotive sector, prototyping stands as a pivotal phase in the manufacturing process, much like in various other industries. Leveraging 3D printing technology significantly enhances the efficiency and speed of prototyping before actual production commences. Through additive manufacturing techniques, prototypes undergo swift and thorough validation, streamlining the overall process.
Pre-Production Sampling and Tooling Optimization
3D printers play a crucial role in preproduction tasks like creating thermoforming tools and molds, as well as rapidly producing fixtures, grips, and jigs. This approach facilitates cost-effective sampling and tool manufacturing, minimizing potential losses associated with high upfront investments in traditional tooling.