The Future of 3D Printing in Patient-Specific Prosthetics and Implants
- Locanam 3D Printing
- Jun 29, 2024
- 3 min read
Medical devices have always been a vision within the healthcare sector. Now advancements in technology are opening doors to innovative digital design and manufacturing techniques, making personalized devices more achievable than ever before.

The combination of computer-aided design (CAD) and additive manufacturing, commonly referred to as 3D printing, attracts significant attention. A major advantage of this combination is its capacity to create Prosthetics objects with more complex designs compared to traditional manufacturing methods. Another appeal lies in the versatility of additive manufacturing, which allows for greater design flexibility and enables quick and cost-effective prototyping.
Implant manufacturing : A new approach
In the coming years, the medical 3D printing industry is poised for remarkable expansion, fueled by factors like customization, reduced production costs, and swift turnarounds. According to Global Data, this market is set to soar from approximately $2 billion in 2022 to an estimated $4 billion by 2026, marking a significant compound annual growth rate (CAGR) of 21%.
As per the data and analytics firm, the future phase of 3D printing’s integration into the healthcare sector is expected to focus on personalized treatments. This could involve producing customized medications inexpensively and creating tailored organs and medical tools directly at the patient’s bedside.
There is a lots of enthusiasm surrounding the potential to address the global shortage of organs by manufacturing these intricate body parts using scaffolds, human cells, and biomaterials. This 3D Printing technology holds promise because it could utilize cells derived from the patient’s own body, thereby reducing the risk of transplant rejection—a significant hurdle in such medical procedures.
3D-printed prostheses?
Prosthetic devices are another area poised to gain advantages from the personalization enabled by 3D printing.
When talking about prostheses and prosthetic liners, the main emphasis is on comfort. These tools are created to assist people in resuming daily tasks and experiencing the independence of moving around without needing a wheelchair. Innovations in 3D printing have enabled the development of diverse designs and internal configurations, allowing for personalized fits for every patient. This personalization guarantees not only a better fit for the prosthetic but also improves overall comfort and usability for the wearer.
Improved shock absorption can greatly benefit patients, reducing the likelihood of scars from medical devices. Through conceptual design, various mechanical properties can be optimized. Utilize 3D printing enables precise adjustments to different parts, ensuring a better fit tailored to individual patients' needs.
You can also blend soft and tough materials within the print by employing various forms of silicone, eliminating the need to put together separate components.
Designs Customized for Orthotics
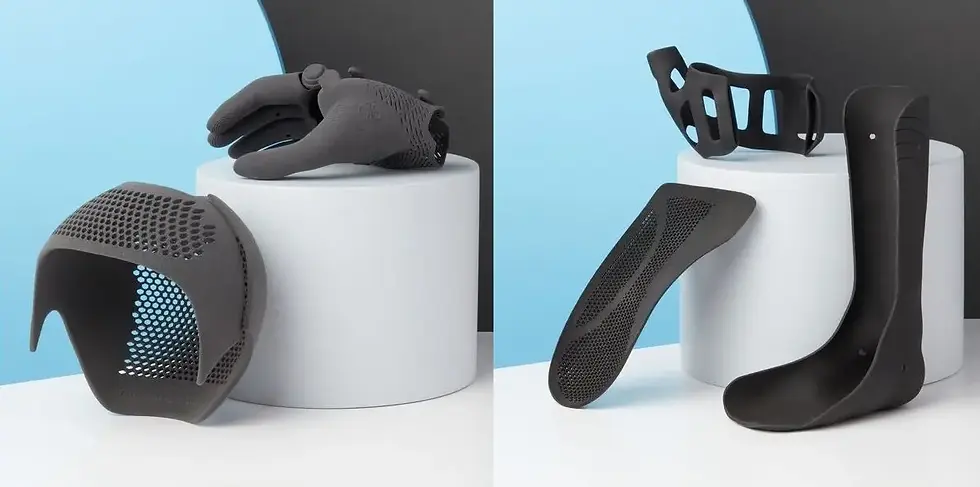
Similarly, these principles are relevant to orthotic devices—a rapidly expanding sector driven by rising diagnoses of diabetes mellitus. Around 60% of these patients develop neuropathy, a condition frequently resulting in foot ulcers.
Customizing the silicone insole's different sections to fit the contours of the patient's foot ensures optimal comfort and effective shock absorption during walking.
Both the orthotics and prosthetics industries are poised to reap rewards from advancements in additive manufacturing and material science. These innovations promise streamlined processes and the development of personalized devices for patients.
For years, silicone has been a preferred material among medical device makers in these sectors. Now, Elkem is investigating how its cutting-edge medical-grade Silbione can be tailored for this advanced manufacturing method.
The outlook for 3D printing appears promising, with silicone set to play a pivotal role in enhancing prosthetics and orthotics applications.
I've been looking for a reliable manufacturing service provider and came across Sogaworks. They offer rapid prototyping manufacturing.