Understanding the Differences between SLA and FDM 3D Printing
- Locanam 3D Printing
- Mar 11, 2024
- 4 min read
Multiple 3D printing methods have been developed over the past few years. These technologies have been rapidly adopted by multiple industries, I am talking about SLA and FDM emerging as two major 3D printing methods. In this article we will discuss and compare these two technologies.
3D Printing Overview
In the last four decades, 3D printing has risen as a pivotal force in the fourth industrial revolution. Today, it's not uncommon to find budget-friendly desktop 3D printers in the hands of enthusiasts globally, churning out a diverse array of commercial goods.
Referred to as additive manufacturing, 3D printing has emerged as a remedy to pressing challenges like housing shortages, organ scarcities, and the democratization of manufacturing processes.
Setting itself apart from traditional subtractive manufacturing, 3D printing boasts several advantages. It reduces waste and expenses by building products layer upon layer from raw materials, ensuring minimal material usage. Moreover, it facilitates intricate designs and allows for the use of various materials in the printing process.
This innovative approach to manufacturing isn't just cost-effective; it's also eco-friendly. Sectors such as construction and space exploration are witnessing a surge in 3D printing adoption.
Since its inception in the mid-1980s, various techniques have been developed, with Stereolithography (SLA) and Fused Deposition Modeling (FDM) emerging as two of the most popular methods.
What is FDM 3D Printing?

Fused Deposition Modeling (FDM) emerged as a significant advancement following Stereolithography in 1989. Since then, it has gained widespread recognition as one of the foremost additive manufacturing techniques employed today. FDM, also known as Fused Filament Fabrication (FFF), stands as a cornerstone for both industrial giants and enthusiastic hobbyists alike, shaping a diverse array of commercial products.
Unlike Stereolithography's utilization of photo-curable resin, FDM operates through a material extrusion process, predominantly employing thermoplastics. This distinction underscores FDM's trademark production process, where thermoplastic filaments are heated to approximately 200°C/392°F and then meticulously layered to mirror the digital blueprint.
The intricacy of FDM lies in its layer-by-layer construction, facilitated by a heated nozzle extruding the filament while the print head maneuvers according to the computerized model. Each layer undergoes a brief cooling phase before subsequent layers are deposited, ensuring precise fabrication until the entire component is realized.
FDM boasts a versatile material palette, featuring PLA, ABS, Nylon, PEEK, and polycarbonate among its common constituents. Notably, ABS reigns as the material of choice in FDM applications, prized for its affordability, robustness, and chemical resilience. Its ubiquitous presence extends from household staples like Lego to a myriad of industrial applications, epitomizing FDM's widespread impact and accessibility.
FDM 3D Printing - Advantage and Disadvantage
Advantage and Disadvantage of FDM 3D Printing Fused Deposition Modeling (FDM), like other 3D printing techniques, comes with its own set of perks and pitfalls that influence its adoption in additive manufacturing. Here looks at its advantages:
Cost-effective Accessibility: FDM stands out as an affordable option, making it an attractive choice for newcomers and DIY enthusiasts alike.
User-Friendly: Its simplicity makes it perfect for those new to 3D printing, facilitating easy experimentation and learning.
Swift Prototyping: Thanks to its straightforward operation, FDM shines in rapid prototyping scenarios, enabling quick iteration and testing of designs.
Disadvantages:
Print Quality Reduction
Slower Operational Speeds in Comparison to Alternatives
Limitations for High-Throughput Industrial Processes
Potential Dimensional Issues like Shrinkage and Warping
What is SLA 3D Printing?
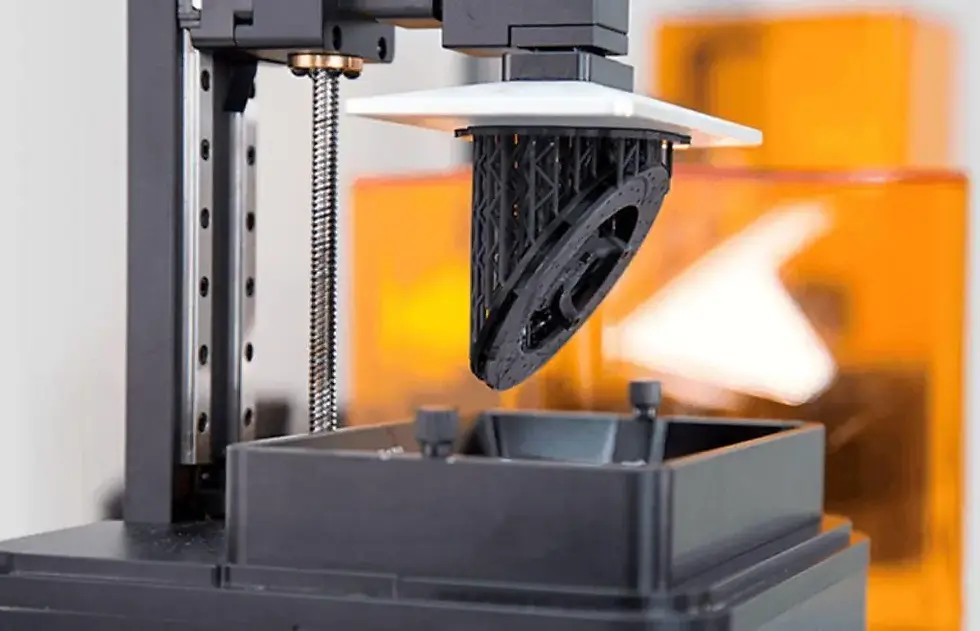
SLA, too known as stereolithography, marks the initiation of 3D printing, accepting its obvious in 1986. It's a spearheading procedure in added substance fabricating, giving rise to advancements like Advanced Light Preparing (DLP).
Operating on the guideline of vat polymerization, SLA makes 3D objects from UV-sensitive gum through photo-polymerization. A light source cements the gum in a vat, and the printer extrudes and stores the laser-cured gum layer by layer to shape the last product.
SLA printers depend on mirrors to direct and center the laser for tar curing. Like other 3D printing strategies, SLA utilizes computer-generated models cut into layers for the printing process.
Within added substance fabricating, two essential SLA printer sorts win: top-down and bottom-up. Whereas top-down approaches overwhelm the field, bottom-up strategies offer interesting points of interest in certain scenarios.
Advantages and Disadvantages of SLA 3D Printing Advantage
Good for complex models
No Human factor
Scalability is simple
Biomedical Molding Application
No Wasted Materials
Relatively fast production
Disadvantage
Parts are affected by moisture, heat, and chemicals
limited to photosensitive resin
Layers cause stair stepping instead of smooth surface
In Conclusion
Stereolithography and Fused Deposition Modeling are two common 3D printing methods, both developed in the 1980s.
SLA and FDM have different uses, each having its own benefits and limitations over the other. For instance, SLA produces more detailed, smoother parts whilst FDM produces more durable and stronger parts. SLA is faster than FDM, whereas FDM can print more colors.
These differences inform the use of each method. SLA is more suitable for high-throughput industrial processes, whereas the limited speed but user-friendliness of FDM makes it more suitable for consumer products, beginners, and hobbyists.
As with any manufacturing method, companies and individuals looking to leverage the environmental, cost, and design freedom benefits of 3D printing should weigh up the benefits and drawbacks of each method before investing time and money in their implementation.
Komentáře