
Inconel Metal 3D Printing- An Overview
Inconel 3D printing utilizes powder bed fusion, commonly known as SLM or DMLS. Highly efficient 3D printing and rapid prototyping service specializing in Inconel nickel alloys, renowned for exceptional temperature resistance.
What is 3D Printing Inconel Metal?
In 1932, the first trademark for Inconel, a groundbreaking superalloy, was registered. Initially employed in the 1940s in the Whittle jet engine, it has since become a crucial component in the aerospace industry, particularly in jet engine combustion chambers. To enhance its resistance to high temperatures, it is often coated with a ceramic material.
​
In contemporary applications, Inconel has expanded its utility to the oil and gas extraction sectors, where its corrosion-resistant properties make it a valuable material for handling corrosive gases. Additionally, Inconel has found its way into NASCAR exhaust systems, showcasing its versatility in diverse industrial applications.
​
And also Inconel finds wide applications in aerospace, owing to its remarkable properties such as high tensile strength, superior fatigue and thermal fatigue resistance, as well as notable corrosion and oxidation resistance. The challenge of working with Inconel lies in its propensity to work-harden during machining. This difficulty is effectively addressed by 3D printing, a process that avoids material work-hardening, making it a favorable option for creating Inconel parts. The primary alloying elements in Inconel include nickel, chromium, and molybdenum. Beyond aerospace, Inconel is also utilized in marine and energy sectors.
Properties of 3D printed Inconel
Inconel, a remarkable superalloy, distinguishes itself through exceptional resistance to oxidation and corrosion, setting it apart in applications within extreme environments like nuclear and aerospace settings.
The corrosion-resistant attributes of Inconel are attributed to the formation of a thick passivation layer through oxidation at elevated temperatures. This characteristic places Inconel in a league of its own when compared to aluminum and steel counterparts.
Oxidation occurs when oxygen interacts with a material, such as metal, potentially leading to rust formation. In contrast, corrosion is the gradual deterioration of a material, which can be caused by acidic environments or various chemicals.
Inconel's superior mechanical properties at high temperatures stem from intermetallic compounds, small cubic crystals in the material that impede slip and creep.
Two prominent alloys in the market, Inconel 718 and 625, exhibit distinct chemical compositions. Inconel 718 includes molybdenum, niobium, tantalum, aluminum, and titanium, while the composition of 625 comprises nickel, chromium, and molybdenum.
The divergence in chemical compositions results in varying properties, particularly in oxidation and corrosion resistance, leading to diverse applications for each alloy.
Inconel 625 finds its niche in jet engines, heat exchangers, turbine rings, and pressure valves, displaying notable resistance to sea water and harsh chemicals.
On the other hand, Inconel 718, with its heightened corrosion resistance, strength, and hardness, proves to be well-suited for applications in the oil and gas industries.
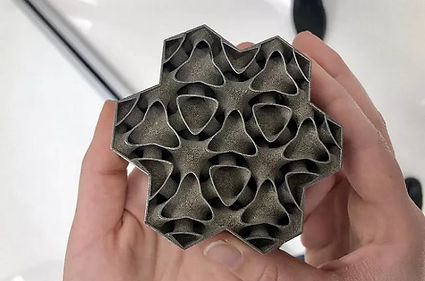
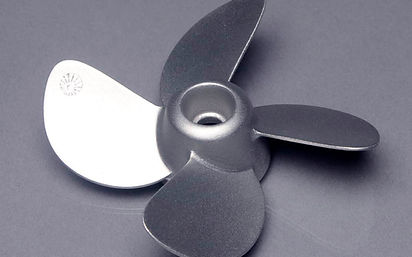
DMLS Inconel 625
This Inconel alloy is fortified with niobium, collaborating with molybdenum to enhance material hardness without relying on precipitation hardening. Renowned for exceptional corrosion and oxidation resistance, it proves ideal for demanding environments like marine, energy, and chemical processing industries. Common applications encompass boat propellers and heat exchanger casings.
DMLS Inconel 718
Inconel 718, renowned for its outstanding high-temperature resistance and strength, retains its mechanical properties even at temperatures reaching 700°C. The alloy can be strengthened through precipitation hardening and is easily weldable. Common uses encompass gas turbine engine components and rocket engines.

Finishes of 3D Printing Inconel
Inconel 3D printing yields components with comparable density to machined parts, and they are conveniently amendable to post-printing processes such as machining or polishing. It's important to recognize that Inconel exhibits work hardening during machining.
​
The standard finishing process entails the elimination of support structures, followed by a medium-blasting treatment to achieve a consistent surface. Optionally, CNC machining or polishing may be applied to specific features, with assessments made on a case-by-case basis.