
Design for Additive Manufacturing (DfAM) is the process of adjusting your CAD design to make it cheaper, faster, or more effective to manufacture. Understand the DfAM and find the best Learn techniques, software tools, and training to apply when creating improved products and components using additive manufacturing (AM) methods.
Additive design offers the flexibility to either adapt a traditional design for 3D printing or create a brand-new design specifically tailored for additive manufacturing (AM) with a Design for Additive Manufacturing (DFAM) approach. In the realm of additive manufacturing, these designs frequently prioritize assembly consolidation and emphasize lightweight structures. This approach lends itself well to biomimicry and intricate geometries, taking advantage of generative design or topology optimization to optimize negative space. The initial stages of additive design involve thoughtful consideration of printing processes, material selection, support structures, and subsequent steps such as depowering and postprocessing.
How to Design for Additive Manufacturing?
Designing for additive manufacturing (AM) encompasses three key areas:
Knowledge of AM Processes and Materials:
It is crucial to have a deep understanding of various 3D printing processes and technologies, ranging from powder bed fusion to stereolithography to material jetting. Each process offers distinct characteristics and design opportunities. Familiarity with the nuances of plastics, metals, ceramics, and other materials during and after the 3D printing stage is essential for effective design.​
DfAM Tools and Mindset:
Utilizing Design for Additive Manufacturing (DfAM) tools, primarily software-based, is integral. Software such as Locanam 3D Printing plays a pivotal role in optimizing computer-aided design (CAD) digital files for additive manufacturing. These tools enable engineers to iterate on part designs, simulate stress factors, generate necessary support structures for 3D printing, and estimate costs and time based on materials and printer capabilities. Adopting a DfAM mindset involves embracing these tools to enhance the design process.

Understanding Design Problems and Opportunities:
An appreciation for the specific design challenges and opportunities presented by AM is fundamental. While there is a wealth of software available for designing for AM, engineers must possess a comprehensive understanding of the intricacies associated with different printing technologies and materials. This knowledge is key to unlocking the full potential of AM in creating innovative and optimized designs.
Additionally, incorporating topology optimization and generative design software, often integrated into CAD and DfAM software, becomes paramount. These tools, exemplified by software from nTopology and Siemens, as well as modules for CAD programs like Solidworks and Creo, facilitate engineers in making intricate calculations for topology optimization. This approach allows for the reduction of required material while maximizing the strength and performance of components.
Benefits of Design for Additive Manufacturing
The numerous benefits of additive manufacturing primarily stem from the remarkable design opportunities that this technology presents.
Design Possibilities:
The revolutionary additive manufacturing process empowers you with unparalleled design freedom, enabling the creation of perfectly tailored parts that align seamlessly with physical constraints. Say goodbye to the limitations of traditional manufacturing methods – embrace the freedom to bring any idea to life. This transformative technology empowers you to push the boundaries of manufacturing, allowing you to break free from the structural and design constraints imposed by conventional techniques. Customize your parts to align precisely with the unique requirements and considerations of your business.
Enhanced Adaptability and Flexibility:
Design for Additive Manufacturing is the key to making your business more adaptable. Take control and adapt every aspect, from the design of your parts to the quantities you produce. The beauty of 3D printing lies in its on-demand production capability – receive parts precisely when you need them. Bid farewell to the need for extensive component storage, as you embrace a more streamlined and flexible approach to production.
Simplified Supply Chain:
The newfound adaptability and flexibility translate into the optimization and simplification of the entire supply chain. A striking example is GE Aviation's use of Design for Additive Manufacturing in 2017, reducing a helicopter engine from 900 parts to just 16. This breakthrough has the potential to significantly reduce the complexity of supply chains, replacing the need for multiple suppliers with the efficiency of additive manufacturing.
Value Addition:
Optimized products and supply chain efficiency become a compelling added value to your business, propelling you ahead of competitors. According to our State of 3D Printing 2020 report, respondents view 3D printing as a powerful competitive advantage. The technology allows for the optimization of every phase of a product's life, from initial development to the production of high-quality finished products.
Time and Cost Savings:
Striking designs not only captivate the eye but also contribute to significant time and cost savings. Whether it's minimizing material usage, avoiding intricate assembly processes, or enabling rapid prototyping, the benefits are numerous. 3D printing has the capability to produce parts that were previously impossible, resulting in superior-performing components and impressive cost reductions. Integrated assembly further accelerates the part conception process, boosting overall company efficiency.
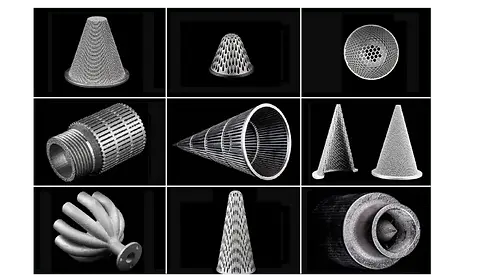

Design for Additive Manufacturing vs Traditional Manufacturing
Traditionally, the design process for CNC milling involves careful consideration of the milling machine's make and model, capabilities, and working volume, which are all machine-driven factors. Additionally, high-tolerance features, tool changes, and setups are influenced by the characteristics of the part being produced.
​
Moving beyond machine- versus part-driven considerations, other details such as spindle speed, materials, and tool type further impact the CNC milling process. The complexity of a part often aligns with the capabilities of a more advanced and expensive machine. Designing for CNC milling necessitates a thorough evaluation of each operation required to produce a part and the corresponding tools needed for those operations.
​
In contrast, designing for 3D printing shares some similarities with traditional manufacturing but introduces unique considerations. 3D printing design involves both process-dependent and printer-dependent factors. As an additive process, 3D printing builds up parts layer by layer, simplifying the number of operations and required tools to just one or two. This eliminates concerns such as tool changes, tool clearance, setups, and custom work holding that are typically part of CNC milling.
​
For instance, a complex part that requires multiple operations, different cutting tools, and setups in CNC milling could be produced with a 3D printer in a single operation, using one tool, and without additional setup. This simplification applies consistently, offering a broad range of design possibilities. However, it's essential to recognize the limitations associated with 3D printing in the design process.
​
One notable advantage of additive manufacturing is that the setup for a complex part is as straightforward as that for a basic one.
​
Consider two part designs as examples: Design #1, a simple part with a vertical hole, and Design #2, which features an angled hole, making it more challenging to manufacture. Design #1, when milled, requires a straightforward machining setup, while Design #2 demands a more complex machine or a more involved fixturing setup. In 3D printing, both designs can be sent to the software, and the printer handles all the setup. Consequently, a geometrically complex part requires the same amount of time and effort to set up as a simpler one.